What Are SMD Components? A Complete Guide for PCBA Industry
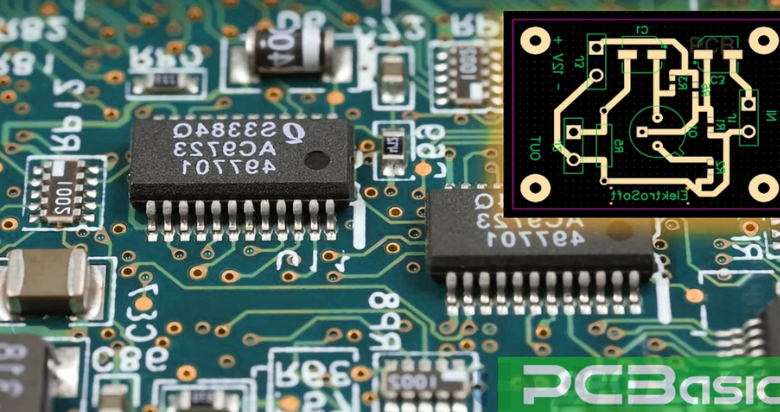
Surface-Mount Devices (SMD components) are the building blocks of modern electronics. From smartphones to automotive systems, SMD components are integral to PCBA (Printed Circuit Board Assembly). Their small size, reliability, and efficiency make them the preferred choice for high-density electronic designs.
In this article, we will explore what SMD components are, their types, advantages, challenges, and their critical role in PCBA manufacturing.
What Are SMD Components?
SMD components are electronic components designed to be mounted directly onto the surface of a PCB (Printed Circuit Board), as opposed to traditional Through-Hole Technology (THT) components, which require drilling holes in the PCB.
These components are smaller, more compact, and easier to assemble using automated processes. SMD technology has revolutionized the PCBA industry by enabling higher packing densities and reducing assembly times.
Key Features of SMD Components:
- Designed for surface mounting without leads extending through the board.
- Compatible with SMT (Surface Mount Technology) assembly processes.
- Typically smaller and lighter than THT components.
Types of SMD Components
- Passive Components
Passive SMD components are non-polarized components that do not require electrical polarity. These include:
- Resistors: Typically in chip resistor packages like 0603, 0805, or 1206.
- Capacitors: Include ceramic, electrolytic, and tantalum capacitors in various SMD sizes.
- Inductors: Often used for filtering and energy storage in power supply circuits.
- Active Components
Active SMD components require electrical polarity to function. Examples include:
- Diodes: SMD diodes like Schottky and Zener diodes.
- Transistors: MOSFETs and BJTs in SOT-23 or SOT-89 packages.
- Integrated Circuits (ICs): From simple logic gates to microcontrollers and processors, ICs are available in QFP, QFN, and BGA packages.
- Electromechanical Components
These include components that involve mechanical movement or switching:
- Connectors: Miniature USB, HDMI, or edge connectors.
- Switches: Tactile and push-button switches in compact SMD formats.
Advantages of SMD Components in PCBA
- Compact Size
SMD components are significantly smaller than their THT counterparts, allowing manufacturers to create compact and lightweight electronic devices. - Automated Assembly
SMDs are ideal for high-speed automated placement using Pick-and-Place machines, reducing human errors and assembly time. - High Reliability
With no lead wires passing through holes, SMD components are less susceptible to mechanical stress, ensuring higher durability and reliability. - Cost Efficiency
Reduced material and labor costs due to automation make SMD components a cost-effective choice for mass production. - Enhanced Circuit Performance
SMD components offer lower parasitic inductance and capacitance, leading to better performance in high-frequency circuits.
Challenges in Using SMD Components
- Assembly Complexity
While automated assembly simplifies the process, handling extremely small components like 0201 or 01005 packages requires precise equipment. - Rework and Repair
Repairing or replacing SMD components is more challenging compared to THT components, especially for components in dense layouts or under BGAs. - Thermal Management
Compact SMD designs can lead to heat concentration, requiring efficient thermal management solutions like heat sinks or thermal vias. - Moisture Sensitivity
Certain SMD components, such as ICs in plastic packages, are sensitive to moisture and require proper storage and handling.
Applications of SMD Components
- Consumer Electronics
- Smartphones, tablets, laptops, and wearable devices rely heavily on SMD technology for compact, lightweight designs.
- Automotive Industry
- Automotive electronics like ADAS (Advanced Driver Assistance Systems), infotainment, and sensors use SMD components for reliability and space-saving.
- Medical Devices
- Compact medical devices such as heart monitors and portable diagnostic equipment leverage SMD components for their small size and reliability.
- Telecommunication
- High-frequency applications in 5G networks and routers depend on SMD technology for signal integrity.
- IoT Devices
- SMD components enable small, battery-efficient IoT devices like smart sensors and connected home appliances.
SMD Components in the PCBA Process
- Solder Paste Printing
- Solder paste is applied to the PCB’s pads using a stencil, ensuring accurate placement for SMD components.
- Pick-and-Place
- Automated machines pick SMD components and place them on the PCB based on pre-programmed coordinates.
- Reflow Soldering
- The board is passed through a reflow oven, where the solder paste melts and bonds the components to the PCB.
- Inspection and Testing
- Inspection methods like Automated Optical Inspection (AOI) and X-ray inspection are used to ensure proper placement and soldering.
SMD Components vs. THT Components
点击图片可查看完整电子表格
Future of SMD Components in PCBA
As electronic devices continue to evolve towards miniaturization and higher performance, the demand for SMD components will only grow. Technologies like chip-scale packages (CSPs) and advanced microelectronics will further push the boundaries of SMD technology, enabling even more compact and efficient designs.
Conclusion
SMD components are at the heart of modern electronics manufacturing. Their compact size, reliability, and suitability for automation make them the backbone of PCBA production. By understanding their types, advantages, and role in the assembly process, manufacturers can maximize their efficiency and deliver cutting-edge products.
If you’re looking for precision SMD assembly and PCBA services, contact us today to learn how we can help streamline your production process!