Coated Screws: Enhancing Durability and Corrosion Resistance
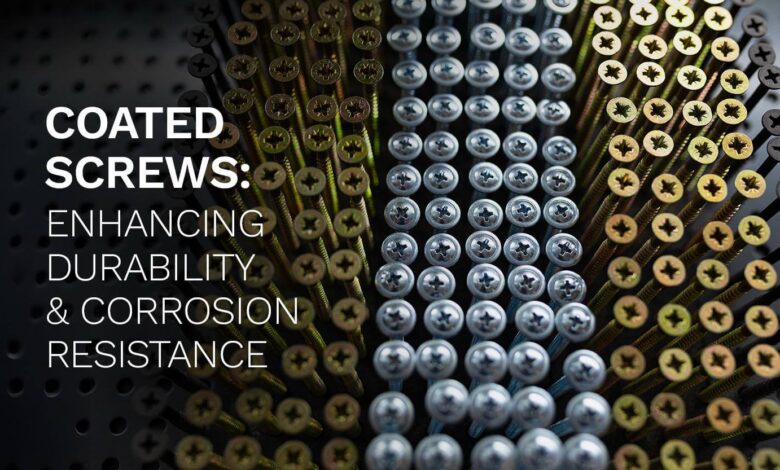
Coated screws are corrosion resistance screws, and are critical components of many industries including construction, automotive, aerospace, manufacturing, and others.
These are used to join two components or structures together. Coatings are generally utilised in screws to improve the durability and performance of the screws. Let’s explore the benefits and details of types of coating in the screws. In this blog, we’ll explore the kinds of coatings available, their benefits, and their applications
What are coated screws?
Coatings are applied to the screws to improve the performance, durability, and corrosion resistance (How to Prevent Corrosion on Stainless Steel Fasteners) of the screws. Varnishes could be organic or inorganic type depending on the screw material and requirements. These coatings can be applied using electroplating, chemical plating, powder plating, or painting. The selection of plating and type of coating depends on the specific requirement and its intended use.
Importance of coating in screws
Before diving into the types of coating used for screws, let’s first understand the importance and role of coating in the screws. Some factors are listed below.
Improves corrosion resistance
Coatings applied to screws primarily aim to improve their corrosion resistance. Screws often encounter harsh environments, including moisture, salt water, and chemicals, which can lead to corrosion and eventual failure. For protection against corrosion coatings such as zinc, nickel, and chrome are commonly used.
Increases wear resistance
Coatings help improve the wear and tear resistance of screws, resulting in increased mechanical strength. For this, coatings such as titanium nitride, diamond-like carbon, and ceramic can enhance the wear resistance of fasteners. These coatings create a hard, smooth surface which helps in extending the life span and reducing friction on screw surfaces.
Provides lubrication
Certain types of coatings provide lubrication to the screws. For example, a coating of zinc and aluminium creates a lubricating film on the screw surface reducing the impact of friction during the installation process.
Enhances appearance
Not just strength, coatings help improve the appearance and aesthetics of screws. Like, decorative chrome or gold plating makes the fasteners look more appealing and luxurious.
Different types of coatings
Nickel Coating:
Nickel coatings are among the most commonly used platings in various industrial applications. These coatings not only improve appearance but also protect against corrosion and increase wear resistance. For more detailed information, refer to this blog: (Why would you choose nickel plating for your fasteners).
Zinc Coating:
Zinc coatings are a widely used method for protecting screws from corrosion. They serve as a sacrificial layer, which means they corrode before the underlying metal does. This type of coating is especially effective in humid environments and is commonly applied through processes such as hot-dip galvanising or electroplating.
Titanium Nitride:
TiN coatings are known for their exceptional wear resistance. They form a hard, durable layer that withstands friction and abrasion, making them ideal for high-stress applications. Additionally, TiN provides an aesthetically pleasing gold-like finish.
Copper Coating:
Applying copper plating not only enhances corrosion resistance but also provides a decorative finish. This type of coating is particularly important in applications where appearance is important, such as decorative fittings or jewellery.
Anodizing:
Anodising is a process of creating a thick and protective, corrosion-resistant oxide layer on a metal part. This type of coating allows for colour customisation, making anodised screws appropriate for visible applications.
Cadmium Coating:
Due to environmental concerns, cadmium coatings are less commonly used nowadays, though it is known or considered for its excellent corrosion resistance and lubrication.
Applications of Coated Screws
Coated screws are used in variety of applications across industries:
1. Construction: In construction industry where exposure to moisture is common, galvanised or zinc-coated screws are often preferred for the robust corrosion resistance.
2. Automotive: For high-performance vehicles that often require exceptional corrosion resistance, TiN coatings are used to match the reliability.
3. Aerospace: Most of the coated screws used in aerospace industry are either zinc-nickel or cadmium coating screws that withstand high-stress while maintaining reliability.
4. Medical Devices: (Hydroxyapatite) HA-coated screws are used in orthopedic equipment due to their biocompatibility and ability to promote bone integration.
Read also: Empowering Technicians with Motorcycle Repair Software
Conclusion
Coated screws are essential for improving durability and resistance to corrosion across various industries. By choosing the right coating tailored to specific environmental conditions and application needs, manufacturers can greatly enhance the performance and lifespan of these critical components. With ongoing technological advancements, innovative coating techniques will continue to evolve, further boosting the functionality and reliability of screws in challenging applications.
In conclusion, whether utilising zinc galvanisation for effective rust protection or advanced coatings such as titanium nitride (TiN) for superior wear resistance, coated screws represent a significant innovation in fastener technology. They play a pivotal role in ensuring safety, efficiency, and durability across diverse sectors. Connect with LP Screw to get superior quality ss screws and superior finish screws for your project-specific requirement.