The Role of Vibrating Screens in Modern Mineral Processing Plants
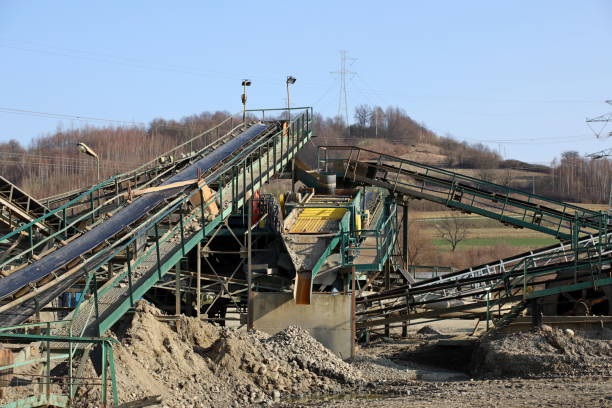
Modern mineral and metal processing operations have become more sophisticated with regard to the technologies and tools used, and most of the valuable sources have been separated and processed using modern conveyer belts and vibrating screens. In these operations, it is among the tools that is very important when it comes to working. Whenever these machines are utilized alongside other vital tools, such as belt conveyor magnetic separation systems, they substantially increase the amount of productivity and improve the quality of the products. This paper highlights how the mineral vibrating screen compliments other technologies in mineral processing plants and their importance.
Importance of Vibrating Screens in Mineral Processing
Vibrating screens are essential components of mineral separation plants because of the nature of their primary functions of sorting and classifying matter. They achieve their functions through particle sifting and classifying using vibrating motions. As a result, the wanted materials are forwarded for further processing and the waste or oversized materials are eliminated.
One of the principal reasons for the importance of vibrating screens is their efficiency in handling large quantities of materials without losing precision. Mineral processing often faces the challenge of high tonnage outputs. Vibrating screens perform well even under heavy workloads, thus enhancing productivity.
They also mitigate the possibility of clogging and ensuring free flow, which is essential for the smooth functioning of downstream equipment. In addition, their compact and modular structure makes them perfect for plants with limited space, thereby improving their versatility. With regard to product quality, vibrating screens ensure that the final output, be it finely crushed ore or larger aggregates used in construction, meets the desired standards.
Their contribution to energy conservation further adds value to their utility. By decreasing the amount of material to be handled, vibrating screens assist in the reduction of dust emissions and energy use. As the mining industry trends towards sustainable practices, these screens are turning out to be an important element in the green mineral processing plants.
How Vibrating Screens Work
The basic operation of a vibrating screen ranges in effectiveness from simple to advanced mechanics. The screen applies vibrations to aid the movement of material on its surface, where smaller particles are deposited in the apertures and the larger ones progress. Motors or eccentric weights are responsible for these vibrations and they serve to facilitate movement of the material in a uniform manner.
These customizations enable operators to make modifications to the vibration frequency and amplitude of the vibrating screens according to the material being processed. This degree of freedom guarantees the best separation of materials regardless of whether dry, wet, fine or coarse materials are handled.
In addition to this, various shapes of vibrating screens such as circular, linear, and elliptical also serve different purposes. Circular ones are appropriate for coarse materials, linear ones are used for fine particles while elliptical ones are efficient with mid-range applications, balancing efficiency and capacity.
While integrating a screen with a belt conveyor and a magnetic separator, benefits surely amplify. The use of vibrating screens guarantees total separation or accurate separation of materials that are then directed towards the magnetic separator, thus, maximally improving the efficiency of the plant which greatly reduces resource loss as well as other handling that is not necessary. Plants aim for smooth and less interrupted material flow, and with the help of vibrating screens, the company’s targets are minimally hindered.
Pros for Modern Plants Using Screens Vibrators
Vibrating screens are able to address all the criteria simply due to their solid construction and versatile designs. This enables the modern minerals processing plants optimal performance along with very little to no maintenance. Some of their benefits include:
Enhanced Efficiency: Only the materials that are required for the next stage are sent forward after splitting, thus, vibrating screens ensure there is a reduced risk of orderly processing which automatically improves the throughput.
Versatility: The limitation of fine powders and other big aggregate does not exist. The range of materials is unlimited which improves operational flexibility.
Durability: The most important feature and utilization for vibrating screens is in mineral processing. The reason for this is because of the rugged design that they are specifically constructed with. Because of this, they are able to tolerate severe conditions like heavy impacts, moisture, and abrasive particles.
Energy Savings: Vibrating screens ensure the smooth material flow while minimizing the need for other unnecessary handling, this helps conserve energy which aids in modern sustainability goals.
Boosted Recovery Rates When coupled with vibrating screens, a belt conveyor magnetic separator increases separation of useful magnetic from non-magnetic materials, thus enhancing recovery rates.
Moreover, vibrating screens are maintenance friendly by design. Their self-cleaning features, durable surfaces, and powerful motors make them extremely reliable even in harsh conditions. With these advantages, vibrating screens form the backbone of efficient mineral processing plants.
The Future of Vibrating Screens for Mineral Processing
The evolution of the mining and mineral processing sector increases the quest for sustainable and efficient technologies. New designs of vibrating screens aim to increase their energy efficiency, output, and ability to work with different materials. More manufacturers are beginning to use modern technologies such as automated control, real monitoring, and self-cleaning screens to improve their vibrating screen’s reliability and use.
A major trend is the integration of digital solutions in the monitoring of screen performance. With sensors placed in screens, metrics such as vibration intensity, throughput rates, and wear patterns can be tracked. This allows operators to make timely adjustments that ensure the best output while reducing the chances of the screen needing repair. These modern features are an essential part of helping the mining industry automate its processes.
As environmental issues become more topical, the industry is also switching to green technologies. This makes it possible for vibrating screens to achieve their intended purpose because they are waste generating. Their combination with belt conveyor magnetic separators achieves resource effective separation that reduces the use of resources. Thereafter, the focus will likely be on the integration of recyclable materials into the designs and reducing the overall energy consumption of vibrating screens.
Conclusion
Vibrating screens have become a fundamental feature in any contemporary mineral processing plant aimed at enhancing efficiency and accuracy. Their importance in bulk material handling cannot be overstated because they classify and separate materials proficiently. Economically and environmentally, installing vibrating screens in systems enhances the processes of waste minimization, throughput optimization, and resource recovery maximization.
The incorporation of applications such as belt conveyor separators and vibrating screens guarantees an efficient process that utilizes time while reducing resource wastage. With advancing technology, the need for plant efficiency will ensure vibrating screens remain in use. For mining companies that wish to be both profitable as well as eco friendly, investing in the latest screeners and separators is not only a suitable option, but a decisive one. These innovations offer immediate value while additionally aiding in the eco-friendly efforts of mineral processing.