Importance of Design for Manufacturability (DFM) in PCB Layout
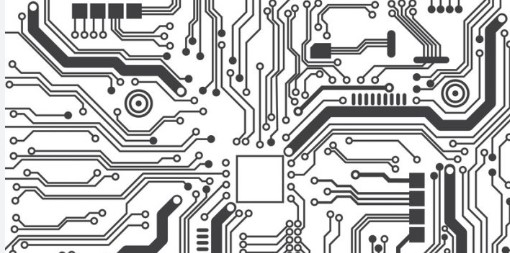
DFM is an incredibly important concept in the field of hardware development and design. It refers to designing products which can be produced with ease. DFM principles for printed circuit boards are also not only about their performance but also about how easy they are to manufacture (manufacturability). These considerations involve recognizing manufacturing’s capabilities and limitations to reduce costs of production, improve quality and shorten time-to-market.
The PCB layout engineer here plays a crucial role in the application of DFM principles. The engineer who understands these principles at the outset of the design hence can anticipate possible areas of manufacturing challenges that he or she will address to avoid them. This enables him or her to avoid doing more than one iteration during the manufacturing stage hence saving time and resources.
Importance of DFM in PCB layout
The significance of DFM in PCB layout cannot be overemphasized enough. It directly affects how efficient and cost-effective the manufacturing process is. Consequently, when designs are made utilizing DFM principles, there is less occurrence of faults during production as well as increased yields. This is especially important in the world of semiconductor companies as even slight increases in yield result in major cost savings.
Another advantage of DFM is that it helps to improve communication between designers and manufacturing personnel. This way both the teams will have agreed on manufacturability constraints and can proceed to achieve the intended results. This is one way to guarantee that the final output has been made to standard without having to complicate the manufacturing process.
Key DFM principles in PCB design:
Some of the most important DFM guidelines that a PCB layout engineer needs to keep in mind are: These principles are geared towards the fact that the PCB layout must be made ready for manufacturing to afford cost and quality.
1. Component placement: The placement of these components is very important to enhance manufacturability. Parts should be arranged in a way that facilitates their connection and subsequent examination. This is done to prevent soldering problems and to allow room for automated assembly tools on the PCB.
2. Trace routing: In this case, trace routing should be done in such a manner that the screen length of important signal paths is short and the routing pattern is simple. This also makes the board easier to manufacture and cuts down on signal integrity problems.
3. Thermal management: Thermal regulation is crucial to avoid short circuits due to the overheating of the components. This includes ensuring the PCB layout’s design provides heat dissipation and does not concentrate heat in certain areas.
4. Panelization: Panelization is where several PCBs are built on a panel to ease manufacturing. Effective penalization can help minimize the wastage of materials and enhance production efficiency.
5. Design rule checking (DRC): Evaluating design rule checks (DRC) from time to time assists in minimizing and solving manufacturability concerns at an earlier design stage. This entails verifying minimum trace width, spacing, and other parameters essential to the functionality of the product.
6. Test points and accessibility: Additional test points and their readiness for testing should be incorporated to maintain quality assurance. This makes it easier to inspect and test the finished PCB than when the pads are formed on the surface of the conductor.
Challenges in implementing DFM
Implementing DFM principles has its challenges despite the numerous benefits that come with it. One of the main obstacles is that the design and manufacturing teams require frequent interaction with one another. An imbalance between these teams can result in designs that are challenging or expensive to produce.
Another problem is that technology changes quite rapidly. This is important because semiconductor companies and PCB manufacturers are regularly incorporating new processes and technologies, meaning that certain DFM guidelines may no longer be relevant. It is thus important that hardware design and development teams keep abreast of these changes to ensure that their designs can still be manufactured.
Furthermore, sometimes it is challenging to achieve an optimal balance between performance and manufacturability. In other words, it is possible that the design, which provides an excellent performance, is difficult to produce and vice versa. Hence, the PCB layout engineer needs to assess the above trade-offs to arrive at the best solution.
Role of software tools in DFM
Software tools are highly essential in the application of DFM principles in the design of PCBs. They help the PCB layout engineers recognize and solve manufacturability problems during the early stages of design. They offer features like automated design rule checks, thermal analysis, and many others that allow for the creation of a layout that is easy for manufacturing.
Newer and more specialized PCB design tools can also model the fabrication process so that engineers can detect imperfections and modify the layout if necessary before fabrication starts. This capability is extremely valuable in hardware design and development where problems can be identified early and rectified before much time is spent on the project.
Read also: The Role of Technology in Shaping India’s Economic Future
Future trends in DFM for PCB design
Several trends may dictate the future of the DFM in the context of the PCB design. One of the most prominent trends is the trend of higher-density PCB layouts. With such an evolution in the technologies used by semiconductor companies, the levels of intricacy in PCB designs are likely to rise. This will imply the use of more complex DFM techniques to deal with the enhanced complexity of the designs.
One trend is increased focus on sustainability as one of the critical factors in manufacturing. New thinking about DFM will be required to take into account environmental problems such as excess production of materials and minimization of energy consumption during product production. This will demand a broader view of DFM, in which manufacturability is only a part of the criterion for optimal design.
Conclusion
To sum up, the incorporation of DFM principles into PCB design layout is a critical necessity for better manufacturability, cost-effectiveness and higher quality designs. If DFM principles are integrated at the early stages of the design process, PCB layout engineers can anticipate possible problems associated with manufacturing, cut production costs and improve product quality. Communication and collaboration between design and manufacturing teams along with the employment of advanced software tools can help to mitigate some of these obstacles.
It is important to understand that hardware design and development is an ever-continuing process, and, therefore, so too is DFM. It will be important for PCB layout engineers to remain abreast of new trends and innovations in the technology to sustain the designing of manufacturable and high-quality PCBs. In conclusion, when effectively implemented, DFM improves the competitiveness of semiconductor companies as it helps them bring better products to the market faster and cheaper.